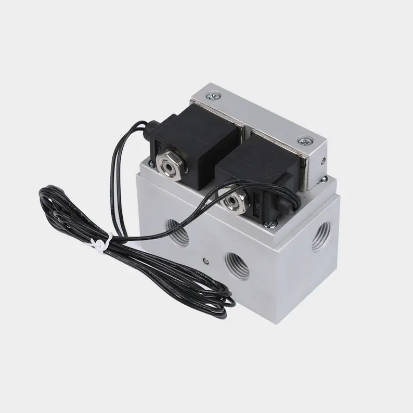
How does this membrane valve use a thin and flexible diaphragm to control fluid flow?
The principle of this Low power consumption high flow rate Membrane valve using a thin and flexible diaphragm to control fluid flow is mainly based on the elastic deformation characteristics of the diaphragm. Specifically, its working principle can be divided into the following steps:
Pressure action: When the fluid passes through the valve, it will generate a certain amount of pressure. Positive pressure will try to deform the membrane in a certain direction, while reverse pressure will try to deform the membrane in the opposite direction. This change in pressure depends on the nature of the fluid, the flow rate, and the design of the valve.
Elastic deformation: The core of the membrane valve lies in its thin and flexible diaphragm, which has superb elasticity and can deform when subjected to pressure. Depending on the direction and magnitude of the fluid pressure, the diaphragm may deform upward, downward, or sideways. This deformation ability allows the membrane valve to adapt to different fluid pressure and flow requirements.
Channel change: As the diaphragm deforms, the size or shape of the channel inside the valve will also change accordingly. When the diaphragm deforms upward, it opens the valve channel and allows the fluid to pass smoothly. Conversely, when the diaphragm deforms downward, it closes or narrows the channel, thereby restricting or preventing the flow of fluid. This change in the channel can be adjusted as needed to meet different fluid control requirements.
Control mechanism: In order to achieve precise control of fluid flow, low-power and high-flow diaphragm valves are usually equipped with advanced control mechanisms. These control mechanisms can be pneumatic actuators, electric actuators, or other types of actuators. They are able to adjust the degree of deformation of the diaphragm according to external control signals (such as pressure, temperature, flow, etc.). These control signals can come from sensors, controllers, or other devices to ensure that the valve can accurately respond to system requirements.
Feedback mechanism: In order to ensure precise control, some diaphragm valves are also equipped with feedback mechanisms. This mechanism can monitor the valve opening, flow, or other relevant parameters in real time and feed this information back to the control system. The control system can adjust the output of the actuator based on these feedback signals to maintain the required fluid flow or pressure. This feedback mechanism enables the diaphragm valve to self-adjust and optimize its performance to adapt to different working conditions and fluid requirements.
In summary, low-power and high-flow diaphragm valves achieve precise control of fluid flow by utilizing the elastic deformation characteristics of thin and flexible diaphragms, combined with control mechanisms and feedback mechanisms. This design gives diaphragm valves obvious advantages in energy efficiency and the ability to handle large amounts of fluid.c