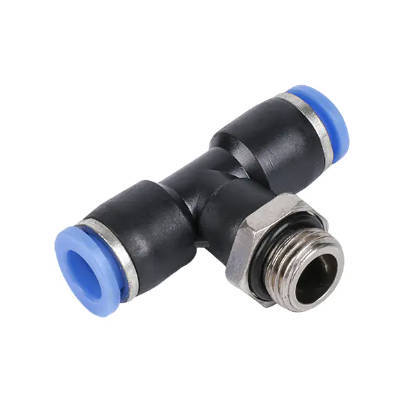
What specific performance benefits do plastic connector materials provide?
Corrosion resistance: Plastic connectors can maintain structural integrity and functional stability for a long time when exposed to corrosive media. This property is particularly important in industries such as the chemical, petroleum, pharmaceutical and food processing industries, which often handle corrosive liquids or gases. Plastic materials such as polypropylene (PP), polyethylene (PE), and polyvinyl chloride (PVC) have excellent chemical stability and can effectively resist the erosion of various chemical substances such as acids, alkalis, salts, and grease.
Lightweight: Compared to metal connectors, plastic connectors are significantly lighter in weight, which is an important advantage for many applications. In the automotive industry, lightweight design is one of the key means to improve fuel efficiency and reduce emissions. The use of plastic connectors helps reduce the overall weight of the vehicle, thereby improving fuel economy. Meanwhile, in aerospace, every gram of weight saved can have a significant impact on flight performance and cost.
Insulation: Plastic materials serve as electrical insulators, making plastic connectors irreplaceable in the electrical and electronic fields. They can effectively isolate current and prevent short circuits and electric shock accidents. In power distribution systems, communications equipment, household appliances and medical equipment, plastic connectors play a key role in ensuring the safe operation of circuits and the reliability of equipment.
Processing flexibility: The processing flexibility of plastic materials provides endless possibilities for the design of plastic connectors. Through various processes such as injection molding, extrusion molding, and blow molding, connectors of various shapes, sizes, and structures can be manufactured to meet the needs of different applications. In addition, the plasticity of plastic materials also allows the addition of various functional elements such as seals, fasteners and guides to the connector to further enhance the performance and reliability of the connector.
Cost-effectiveness: The low cost of plastic materials and efficient production processes give plastic connectors significant advantages in cost control. Compared with metal connectors, plastic connectors have lower raw material costs, shorter production cycles, and higher production efficiency. This helps reduce product manufacturing costs and improve market competitiveness. At the same time, the maintenance and replacement costs of plastic connectors are relatively low, reducing the user's total cost of ownership.
Impact resistance: Certain types of plastic materials have excellent impact resistance and are able to maintain structural integrity and stability when impacted by external forces. This characteristic is particularly important in applications that need to withstand vibration or shock, such as pipe connections in automobile engine compartments and hydraulic systems in industrial equipment. The impact resistance of plastic connectors helps reduce damage and failure due to vibration or shock, increasing system reliability and service life.
Good sealing: Plastic connectors are usually designed with a precise sealing structure to ensure that no leakage of fluid or gas occurs during the connection process. This good sealing performance is of great significance to maintain the normal operation of the system and prevent environmental pollution. In industries such as chemical, pharmaceutical and food processing, the sealing performance of plastic connectors is directly related to product quality and safety.
Easy to install and maintain: Plastic connectors usually adopt simple and fast installation methods, such as snap-on, threaded or quick-plug types, making the installation and removal process more convenient and faster. This design not only reduces installation costs and time, but also improves maintenance convenience and efficiency. The ease of installation and maintenance of plastic connectors is particularly important in applications that require frequent connector replacement or adjustments.